Competence and expertise in coil coating technologies
Our surface finishes offer wide-ranging benefits: In addition to unrivalled material qualities, the use of pretreated coil metals or panel blanks results in significant cost advantages in the production process. Our products are immediately ready for use and are ready for printing, back-injection moulding with plastic or for use in the laminates industry without any additional work steps.
Tailored product qualities for the highest standards

Scratch resistance

Patterns/Colours

Printable

Ready to use HPL/CPL

Long-term stability

Maximum reflectivity/high absorbency

Formable
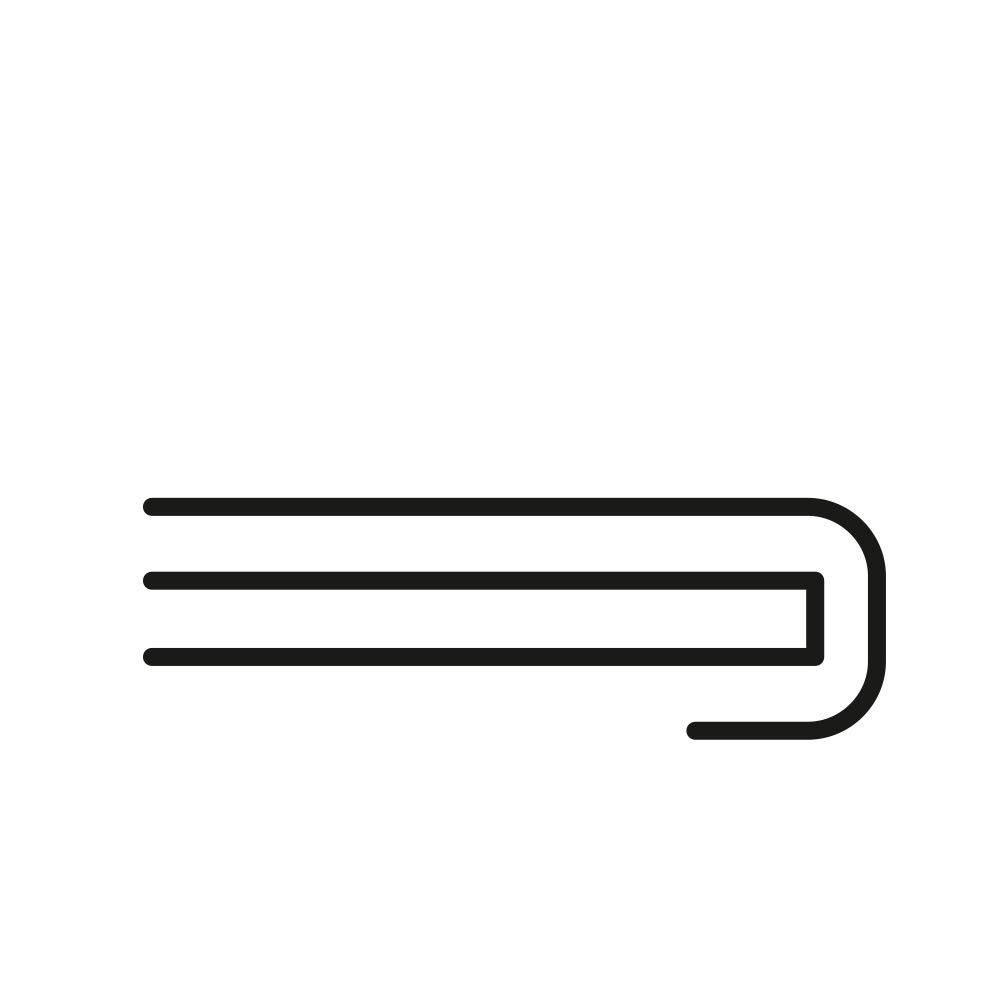
Electrical conductivity/insulation
Video about the Alanod high-end lacquering line

Anodising
Electrical oxidation of metal surfaces is called anodising. This involves an electrochemical process to systematically transform the aluminium surface into aluminium oxide (Al2O3) in its glass-like state. Unlike applied lacquer coatings, the resulting coating is an integral part of the initial material. It is as hard as ceramic, highly transparent and offers the possibility to reliably incorporate colours. Anodised aluminium surfaces are therefore used wherever long-term stable, resistant surfaces and a decorative appearance is required

PVD coating
PVD stands for Physical Vapour Deposition. In principle, metallic materials are vaporised and the resulting metal ions condense on the substrate – in our case the coil metal surface – to form a thin coating.This results in surfaces that are not only decorative but also boast excellent optical properties. PVD-coated metals are therefore used in the electronics, lighting and solar industries.
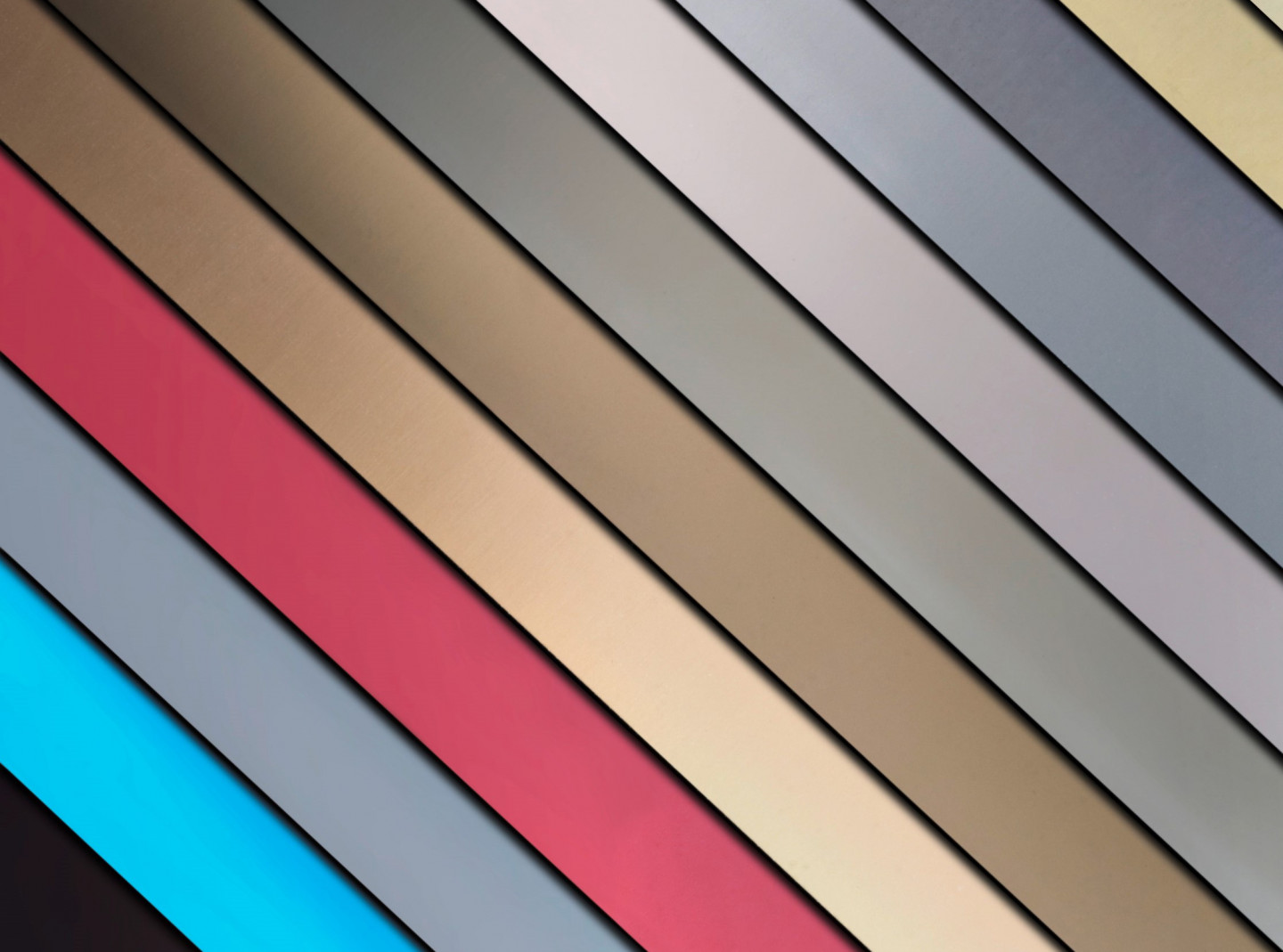
Primer lacquer systems
Our modern lacquering system rounds off the decorative and technical applications for our products. Using the coil-to-coil method, aluminium and other metal coils can be refined with highly transparent, clear lacquer systems by roller application, which improves the anti-corrosion protection with only a minimal reflection loss. Opaque or translucent stoving lacquers can give our material a unique decorative character. In addition, functional lacquers give our products qualities such as scratch resistance, chemical resistance and anti-fingerprinting. What’s more, by applying special primer systems, it is possible to further process our products using co-injection moulding with plastics, or laminating them with phenolic resin-impregnated papers.